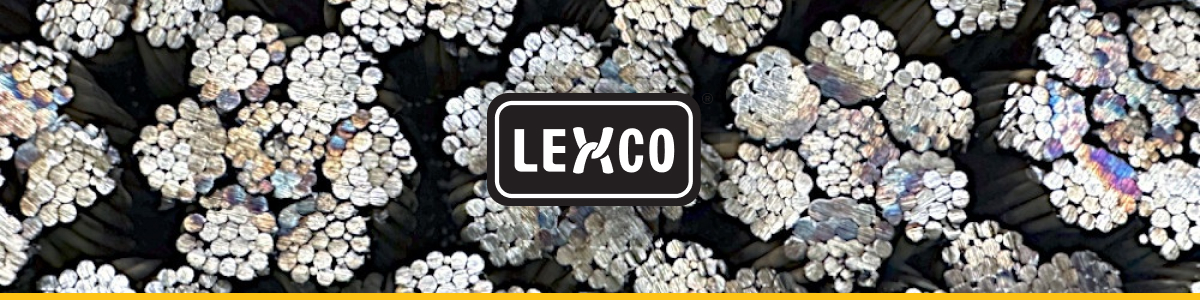
Wire Rope 101
Wire rope is used in a number of different applications, both in commercial and personal projects.
It is relied on for its strength, flexibility, and ability to transmit forces or energy in a predetermined manner. It’s incredibly useful and versatile.
Here, you’ll find everything you need to know about wire rope – a starting point for anyone interested in learning the basics of this impressive material.
As with any machine, the proper usage and functional characteristics of wire rope must be recognized to maximize its longevity.
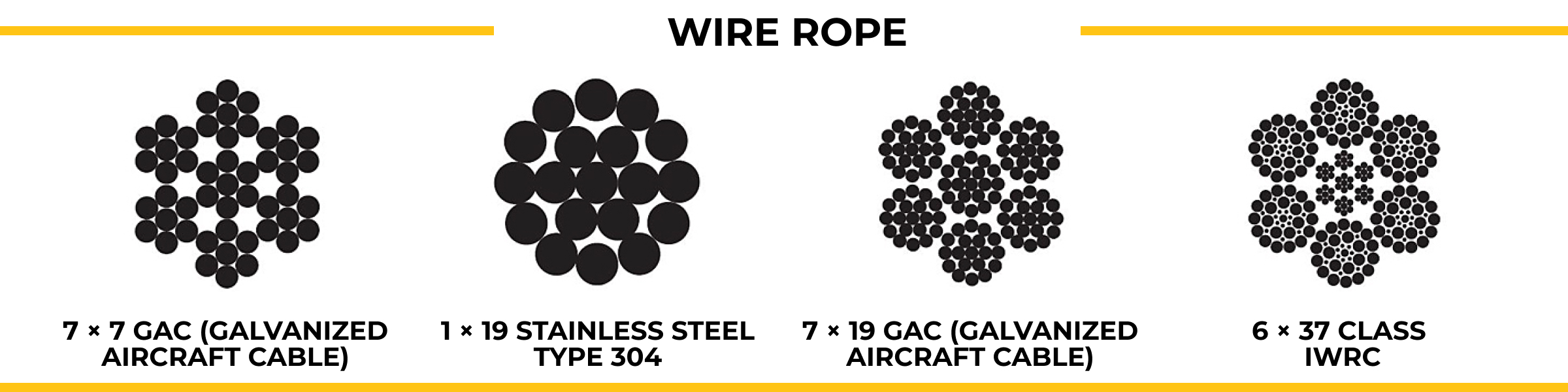
What is wire rope?
Wire rope is a multi-wired stranded length of rope, wherein a core member has had other multi-wired strands laid over it.
In technical terms, wire rope is referred to as a ‘machine’ in and of itself, based on the technical definition of one. This is due to the fact that the configuration and way that it’s made, combined with the careful selection of materials, enables wire rope to transmit motion, energy, and other forces toward a desired end. In that way, it is considered a machine.
‘Wire rope’ and ‘cable’ are sometimes used interchangeably. However, wire rope usually designates lengths with a diameter larger than ⅜ inch. When the diameter of the wire dips below that threshold, it is called a cable or cord.
While there are some more frequently used materials for wire ropes, with the most common being high-carbon steel, wire rope can be made up of steel, iron, monel, bronze, stainless steel, and more. Manufacturers usually choose wire rope based on the material that’s going to withstand what the rope will be used for in a given application.
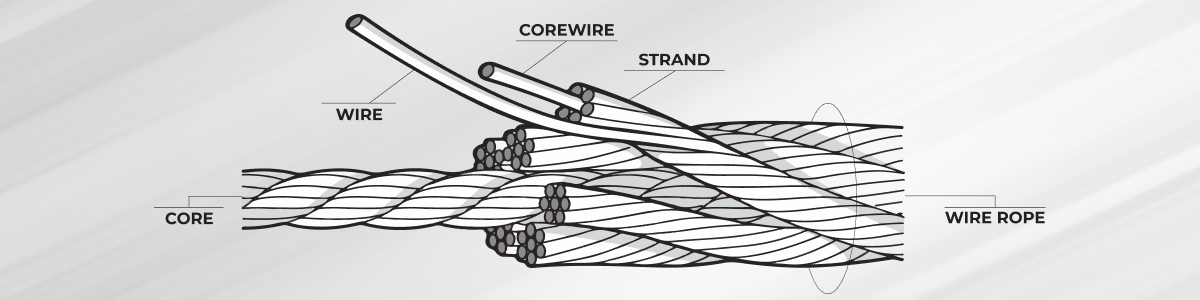
What’s inside wire rope?
Strands
One of the defining characteristics of wire rope is that it comprises an assembly of ‘strands.’ Each strand is two or more lengths that have been laid in a concentric pattern around a center wire, usually consisting of one or more layers. Most commercial strands are made of 7, 19, or 37 wires each, though other constructions exist.
From there, a group of strands are laid helically around a central core. That core may be comprised of fiber or steel, though it is occasionally a combination of the two. The final product is what we know as wire rope.
When it comes to product designation in wire ropes, the notation uses the number of wires and the number of strands as a metric. A wire rope consisting of 7 strands, with 19 wires in each strand, would be designated as 7×19.
The more wires in a strand of a given diameter, the more flexible the final product will be. A 1 x 7 rope will be fairly stiff, whereas a 7 x 19 configuration will be highly flexible, and is excellent for use in pulley systems where it will need to be curved continuously.
Lay direction
Strand lay direction is a term used to discuss which direction the strands are laid in relation to the direction of the outer wires, taking into account the longitudinal axis of the strand itself. Multiple orientation lay patterns occur when at least two layers of wires are contained in successive layers and laid in more than one operational direction.
Right lay means that the strands have been passed over from left to right across the length of the wire rope, and left denotes the opposite.
The terms ‘lang lay’ and ‘regular lay’ refer to how these wires are configured within each strand itself. ‘Regular’ means that the wires have been arranged opposing the lay of the strands. Lang lay, on the other hand, means that they’ve been set up in the same direction.
Right lay, regular lay is the most commonly seen configuration of wire rope, as it has a vast array of possibilities.
Cores
The core provides a source of support for the wire rope and maintains the outer strands’ overall position when it’s in motion or being otherwise used.
The usual terminology surrounding wire ropes will include information about the core of the rope around which the strands are laid. A few wire rope core types are as follows:
- Fiber, or FC – made of natural materials and fibers
- Solid polymer core – a singular piece of solid, cylindrical material that makes up the center of a wire rope. It may also be grooved.
- Steel, or Independent Wire Rope Core (IWRC) – In this case, the rounded wire rope core is made of steel, or of wire strands itself.
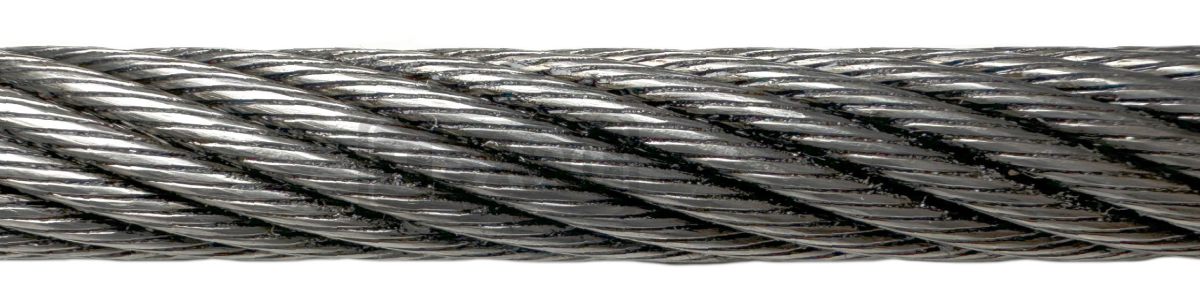
Fundamentals of wire rope
Materials
Different manufacturers will need their wire ropes to be able to perform varying jobs. Flexibility, corrosion resistance, strength, breaking point, and more are all things that professionals take into account when selecting the materials their wire rope is made. Two popular materials are stainless steel and galvanized carbon steel.
Stainless steel
When corrosion resistance is a must, stainless steel is the material of choice. 302-grade stainless steel, a combination of 18% chromium and 8% alloy, is a commonly accepted grade because it is highly resistant to corrosion and boasts excellent strength.
Additional grades of stainless steel used in wire rope include 304, 305, 316, and 321. 305 in particular, is perfect when the application needs to make use of its non-magnetic properties.
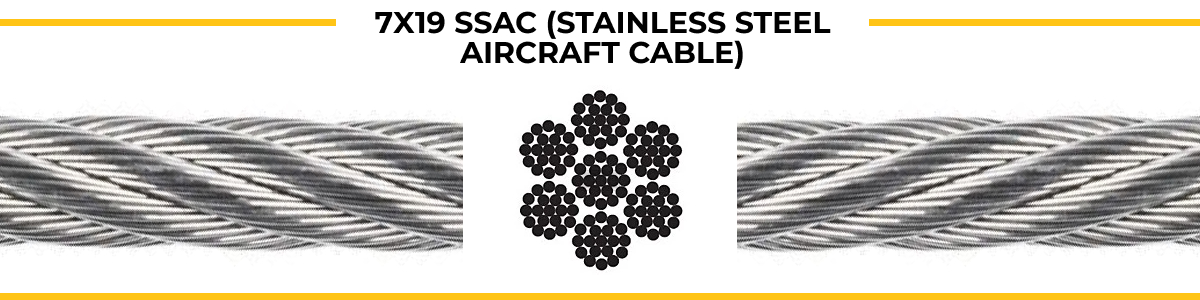
Galvanized carbon steel
Galvanized wire rope is the go-to for wire rope that will be used in instances where high strength is necessary. It also tends to be less expensive than stainless steel wire rope. In this type of wire rope, the wires are individually wrapped with a layer of zinc, which can supply a substantial amount of corrosion resistance.
Construction
The way strands are constructed within the wire rope can change the way they handle fatigue, abrasion, crushing, and other applications.
- Single size: This is the basic type of strand construction in which the strands and core are roughly the same diameter.
- Seale: Larger outer wires wrap themselves around a layer of the same number of inner wires, which surround a core.
- Filler Wire: In a ‘filler wire’ construction, small wires fill the spaces between larger ones, usually in favor of crushing resistance.
- Warrington: The outer layer comprises alternating large and small-diameter wires, which makes for excellent flexibility.
Extrusions and finishes
Wire rope is sometimes referred to as aircraft cable. This is usually due to the fact that it is often used for applications within the aerospace industry. In order to protect the cable and change the outer profile of the cable itself, those cables can be coated in a layer of polyvinyl chloride (PVC), high-density polyethylene (HDPE), or nylon.
Coating wire rope and aircraft cable is done for several reasons; usually, it is to protect the wire, make it more visible in situations where seeing the rope will help deliver a message about its use, enable better ergonomics, and for aesthetic purposes.
Bending
All wire ropes, save for those specifically designed to be entirely stationary, will be subject to be bent and manipulated, either as part of their desired intent or in storage or transport around drums. As stated, wire rope is considered a machine by definition: the individual elements, the wires and strands, will slide along each other when the rope is vent. Lubrication is vital to ensuring that wire rope continues to function correctly and extend its longevity.
Bending can have two significant impacts on wire rope: loss of strength and fatigue. Loss of strength occurs when the wires cannot adjust themselves into their new, changed positions upon being bent out of shape. Repetitive flexing will begin to develop ‘bending loads,’ which will grow into points of stress concentration.
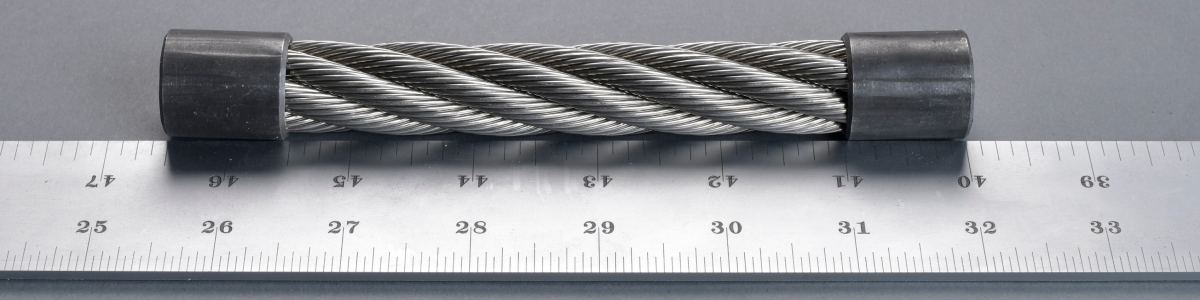
The Wire Rope Experts
We at Lexco® Cable take immense pride in our products. Wire rope is what we do, and we do it well. All of our wire rope is carefully engineered and meticulously inspected to ensure longevity, quality, and durability. Our large facilities make it so that we can efficiently meet the needs of our customers’ custom wire rope orders.
Contact us today to learn more about finding a suitable wire rope for your next project.