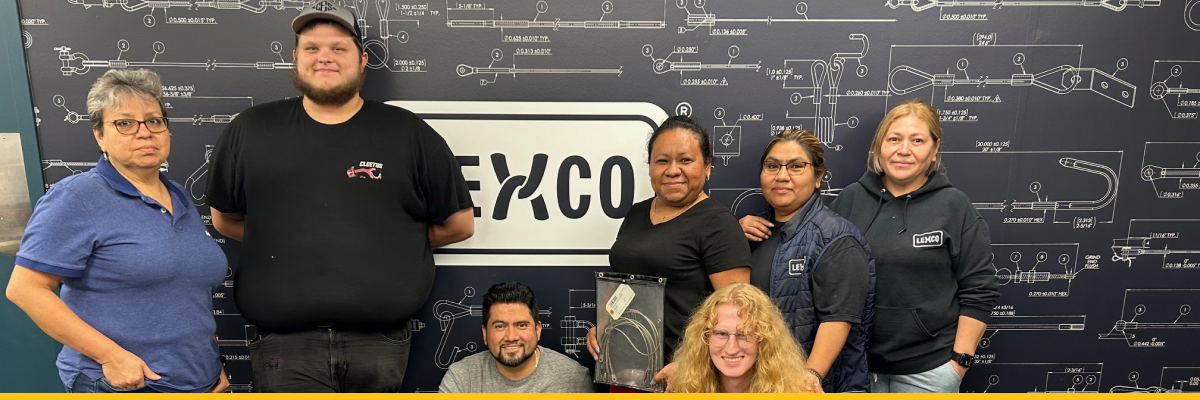
Lexco Cable® Adopts the 5S Method for Enhanced Organization and Efficiency
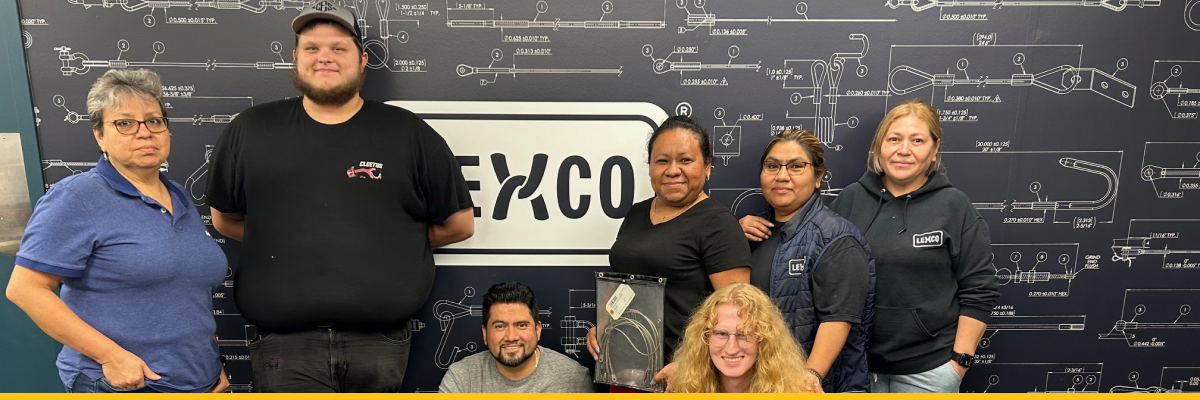
Lexco Cable® Adopts the 5S Method for Enhanced Organization and Efficiency
At Lexco Cable, innovation and continuous improvement are key drivers of our success. We’re proud to announce the implementation of the 5S method—an organizational strategy rooted in Lean Manufacturing. Designed to maximize productivity while minimizing waste, the 5S methodology focuses on five key principles: Sort, Set in Order, Shine, Standardize, and Sustain. This approach aligns with our commitment to improving efficiency, delivering high-quality products, and ensuring customer satisfaction.
Taking Lessons into Action
To introduce the 5S methodology, our team began by reorganizing a designated workspace area. Employees assessed tools and materials, determining their usage frequency—daily, weekly, or monthly—and removed unnecessary items. Items potentially reused were relocated to other areas, while truly obsolete items were responsibly discarded. This process is essential for decluttering and saving time, allowing employees to focus on production tasks rather than searching for misplaced tools. To further streamline operations, red-and-white striped tape was introduced to delineate machine zones and corresponding toolboxes. This simple measure ensures tools and equipment are always in their proper place, enhancing accessibility and reducing downtime.
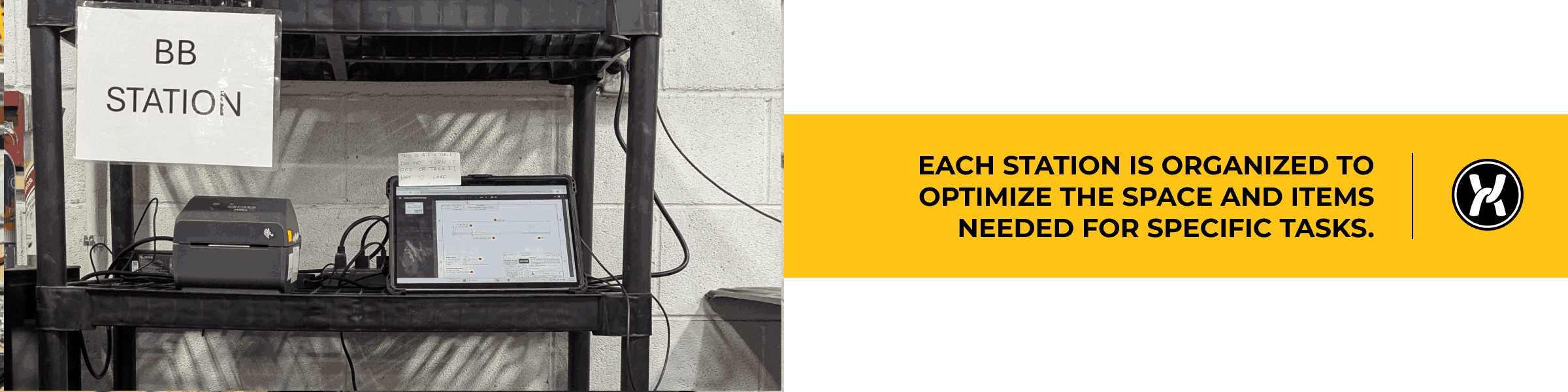
Early Success
The initial implementation has already yielded positive results. Employees report improved efficiency, as well as an increased sense of accountability for maintaining clean and organized workstations. According to the team, the 5S approach has reduced the time spent searching for tools and fostered a safer work environment by eliminating hazards. Some of the Lexco team members stated,
“A clean and organized area speeds up work hours and minimizes wasted time.” – Noe Taboada, Production Manager
“The 5S system helps to eliminate distractions and improves focus.” – Jadwiga Mirowski, Engineering Manager
Managers are now empowered to assess and adjust workspaces more effectively, ensuring every tool and resource has a designated spot.
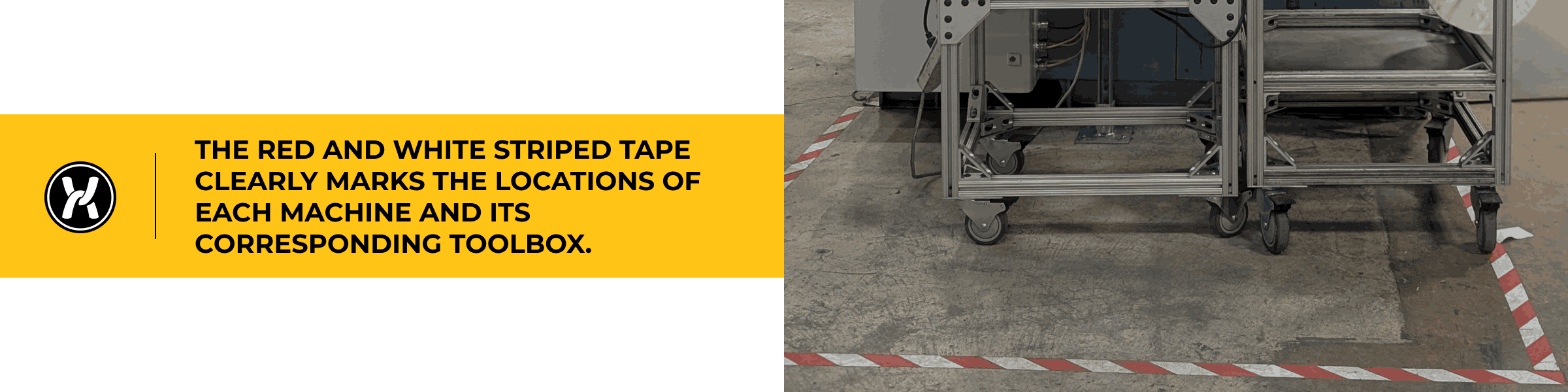
Looking Ahead
Lexco plans to expand 5S across the entire organization, beginning with other production sections and eventually extending to all operational areas. This strategic rollout will be guided by a schedule, prioritizing high-impact zones to maximize benefits early in the process.
Adopting the 5S methodology reflects Lexco’s dedication to fostering a culture of continuous improvement. Beyond production efficiency, this initiative instills valuable organizational habits that resonate across all workspaces.
We’re excited to see the positive changes brought by 5S and look forward to implementing these strategies across the company.
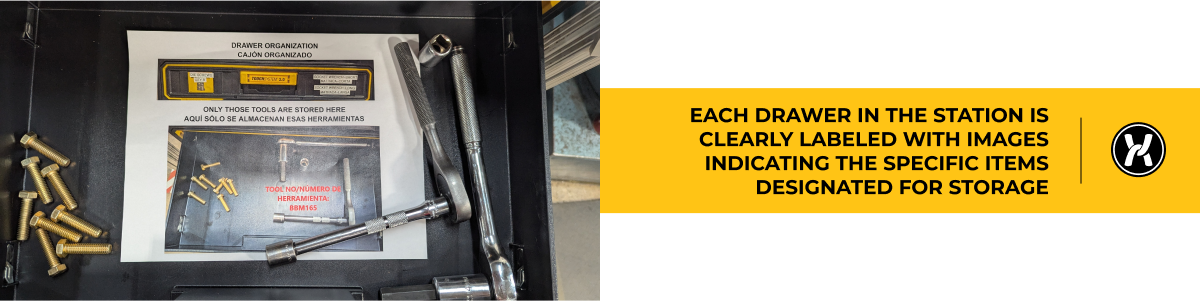