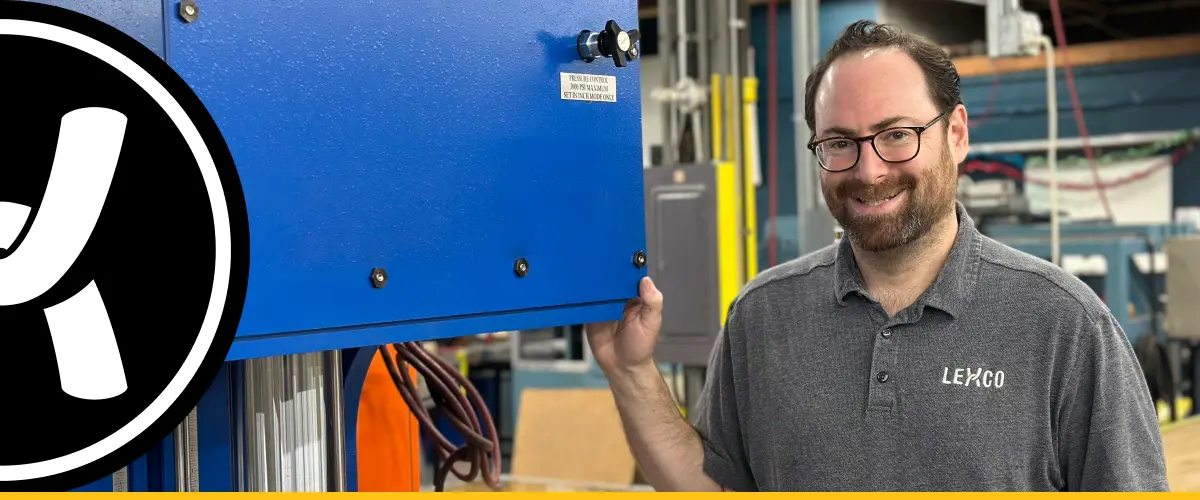
Lexco Cable® Expands In-House Capabilities with New Press & Laser Machines
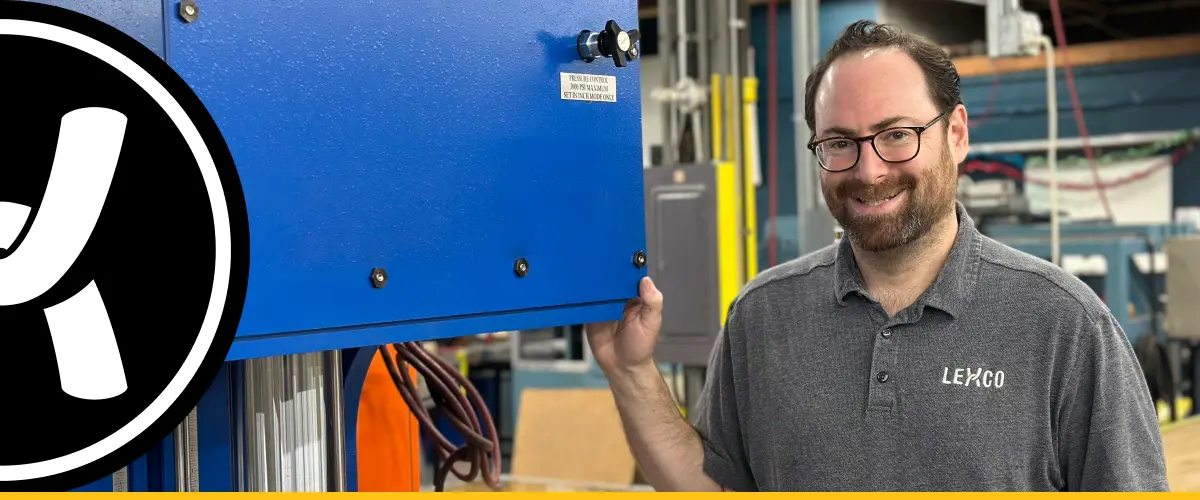
Lexco Cable® Expands In-House Capabilities with New Press & Laser Machines
Lexco continues to invest in tools that help deliver speed, precision, and flexibility. Two new machines, a high-speed 50-ton press, and an upgraded laser marker, have recently joined the Lexco production floor, further enhancing what the team can accomplish in-house and on deadline.
Laser Etching with Accuracy and Efficiency
Lexco’s new laser etching system brings a significant upgrade in speed and capability, offering enhanced performance for high-volume and custom marking needs. The new machine marks more assemblies and tags per minute, thanks to a more powerful beam and faster processing speed.
One of the most notable enhancements is the laser’s ability to produce higher contrast markings on a wider range of materials. Surfaces that previously posed challenges such as certain metals or coated finishes can now be etched with greater clarity and precision. This ensures long-lasting legibility for critical markings like serial numbers, barcodes, logos, and part identifiers.
The machine is also mounted on a larger custom cabinet that accommodates bigger parts and assemblies than before, broadening the range of products Lexco can process in-house. This added flexibility eliminates the need for custom fixturing or third-party marking, keeping jobs moving efficiently and under Lexco’s quality control.
The new system also features upgraded software and a more intuitive user interface, making it easier for technicians to store and retrieve customer-specific programs. These improvements speed up job setup, simplify repeat orders, and support faster training for new team members.
A Powerful Upgrade for Cable Loop & Eyelet Assemblies
Lexco’s newly installed 50-ton press is a powerful addition to the production floor, combining strength with speed and efficiency. What sets this machine apart is its stroke speed, it operates nearly as fast as a 20-ton press, giving the advantage of high tonnage without the slower cycle times typically associated with larger presses. This boost in speed translates directly into increased output, enabling more assemblies to be completed in less time, particularly in high-volume production runs.
Engineered to handle 1/8″ stamped eyelet assemblies and smaller, the press supports materials such as zinc-plated steel and stainless steel with precision and consistency. It’s also capable of producing loop assemblies in larger diameters, including 3/16″ and 1/4″, using aluminum or copper fittings. This expanded forming range enhances Lexco’s flexibility to meet a variety of customer requirements, from compact eyelet terminations to heavy-duty loop applications without additional machine setups or delays.
Strategically positioned, the press helps streamline internal workflow and reduces inter-building transfers that can slow production. It’s a smart addition that allows the team to scale operations while maintaining the tight turnaround times Lexco is known for.
Delivering More In-House
These upgrades reflect a broader focus on giving customers more speed, more precision, and more capabilities while staying responsive to project-specific needs. By expanding the capacity of what can be handled internally, Lexco continues to provide a high level of control over quality, timelines, and customization.
Whether you’re sourcing assemblies for aerospace, architecture, fitness, or industrial applications, Lexco’s growing equipment portfolio helps ensure the tools and the team are ready for what’s next. Learn more about Lexco’s capabilities at https://www.lexcocable.com/about-us/capabilities-services/
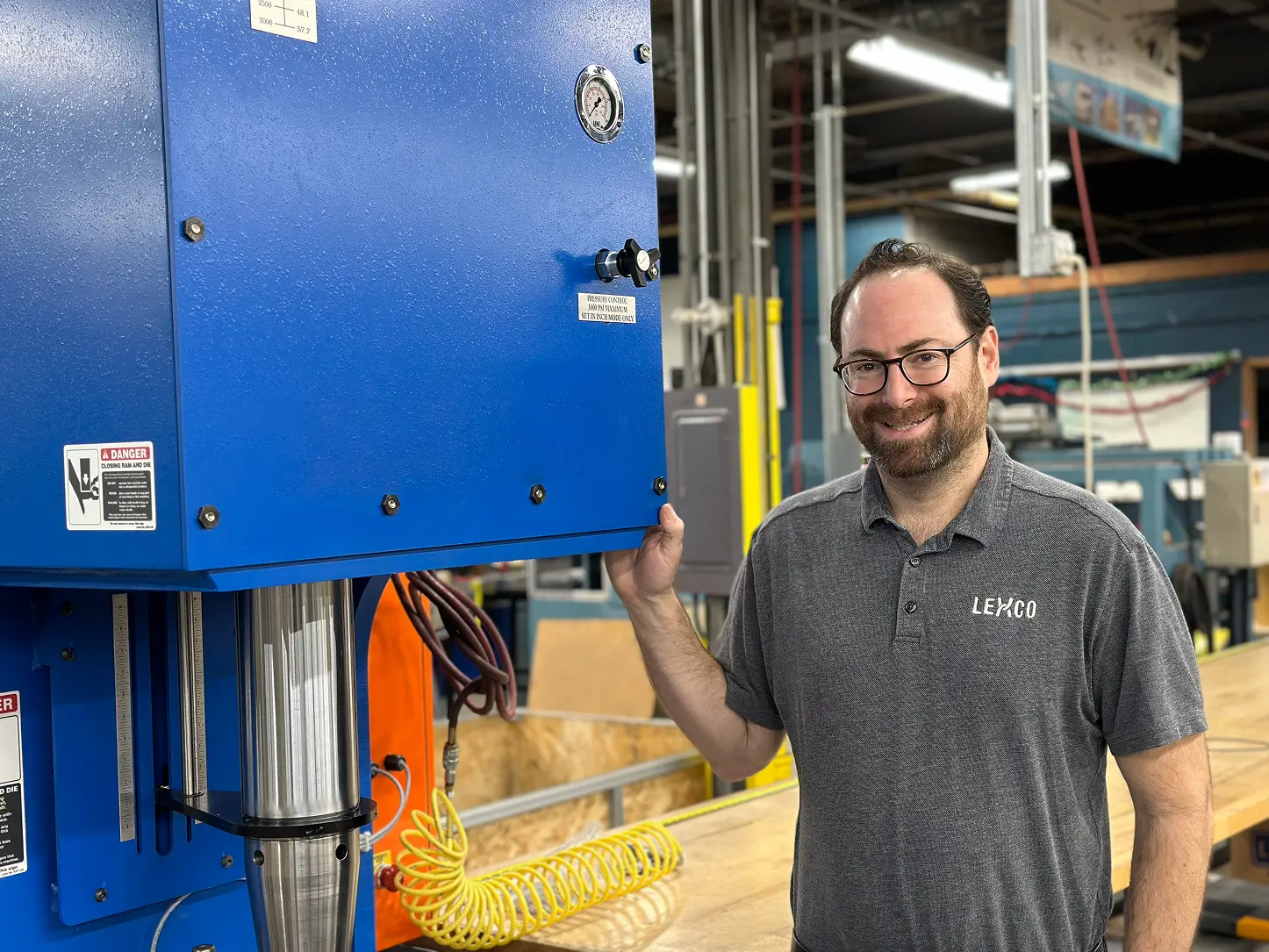
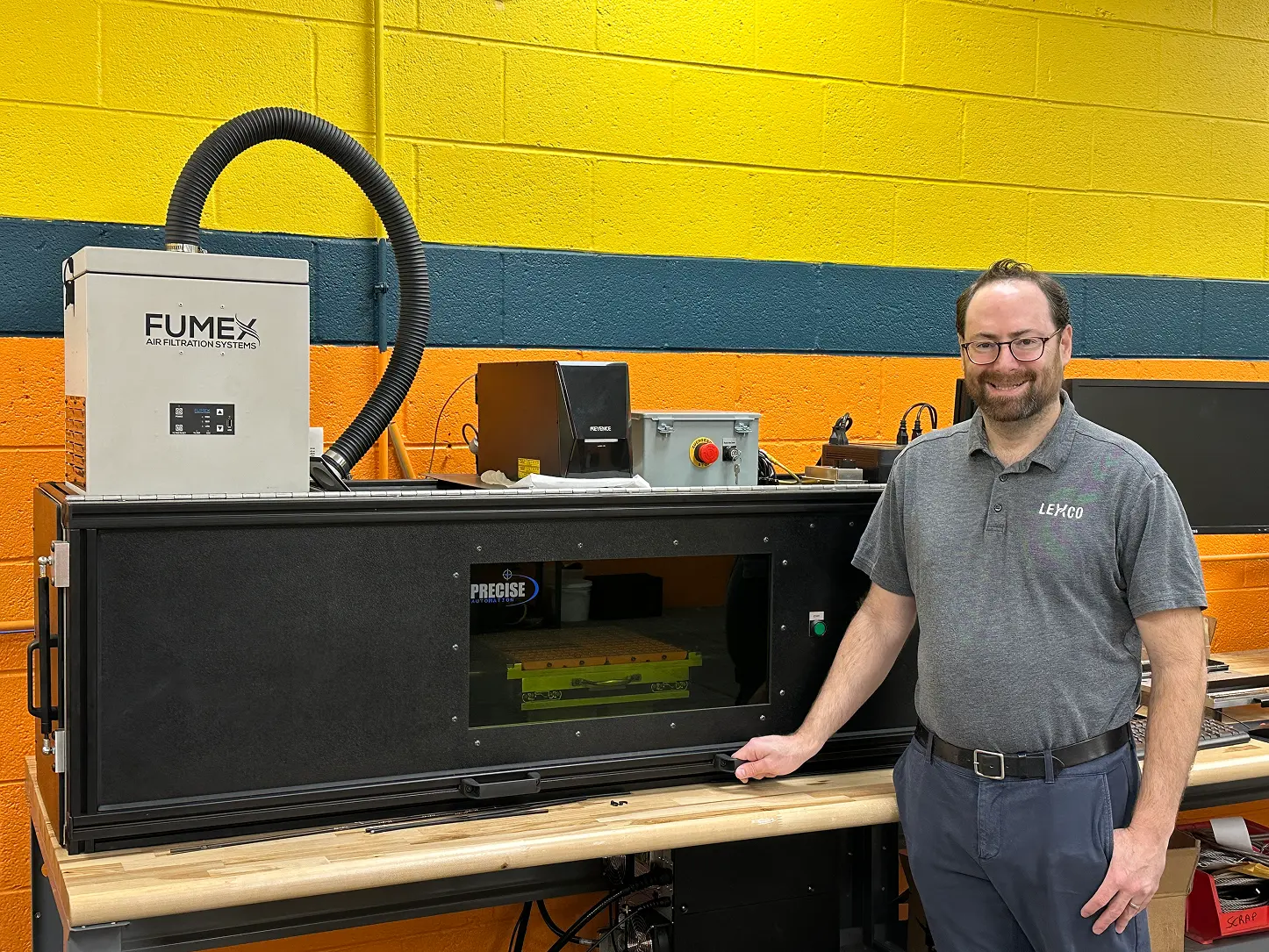