Modernizing Lexco® Cable’s Operations with Masterplan ERP
Lexco Cable, a leading provider of wire rope and cable assemblies, had reached a critical time in its growth journey. Legacy systems that relied heavily on paper processes were no longer sufficient for the company’s needs. To transform its operations and improve customer experiences, Lexco implemented the Masterplan ERP system.
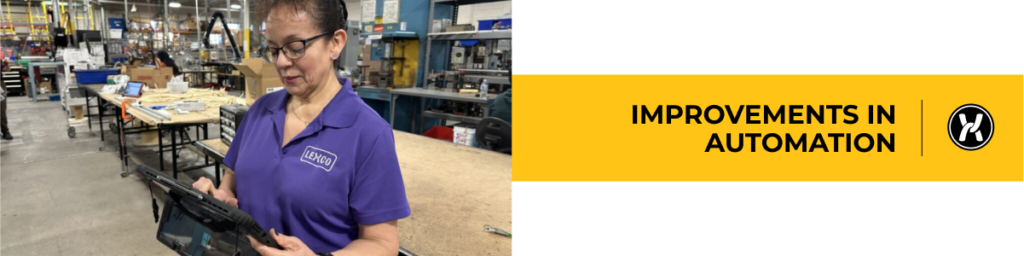
Improvements in Automation
One of the most significant changes in the ERP process was the move to paperless workflows. Previously, departments had to rely on printed documents for tasks such as processing orders and tracking engineering reviews. With the ERP, all workflows became digitized and automated, enabling seamless collaboration between departments. The system automatically triggers engineering workflows for orders requiring review, complete with clear traceability to the assigned engineer and the progress of the task.
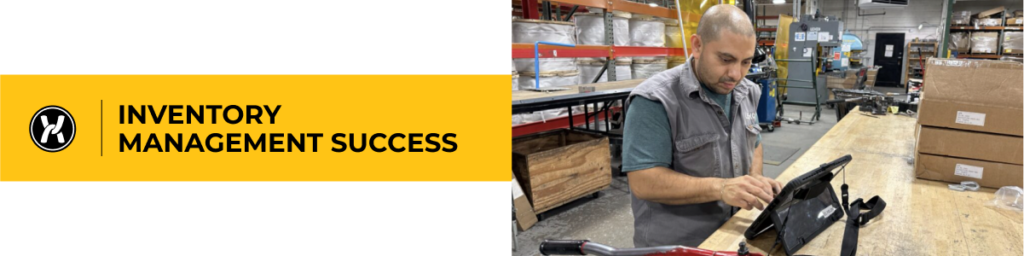
Inventory Management Success
Inventory management also saw dramatic improvements. Before the ERP, employees faced the time-consuming task of locating inventory manually. Now, with the implementation of reel identifiers, staff can access real-time information about reel lengths and locations directly from the ERP. This enhancement streamlined order fulfillment, particularly for custom cable lengths that required precise inventory data.
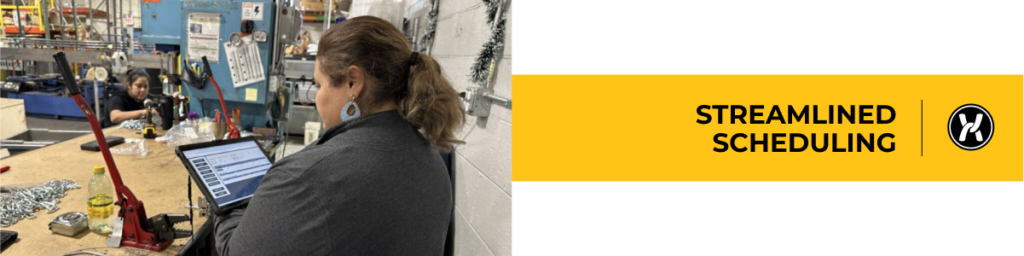
Streamlined Scheduling
The ERP also improved scheduling. Previously, scheduling was managed in a separate system; by integrating scheduling with production and inventory data, the ERP reduced manual data entry and improved the accuracy of production planning. Engineers also benefited from automation, as repeat orders can now bypass manual processing unless revisions are required. This allows the engineering team to focus on new and complex orders, increasing overall capacity.

Customer Service and Cyber Security Wins
Beyond operational improvements, the ERP also enhanced Lexco’s customer service capabilities. Customers benefited from faster access to documents like certifications, shipping records, and inspection reports, which are now stored digitally within the ERP. Customers also benefit from increased cyber security. The ERP data is hosted on AWS servers which can keep even sensitive data secure.
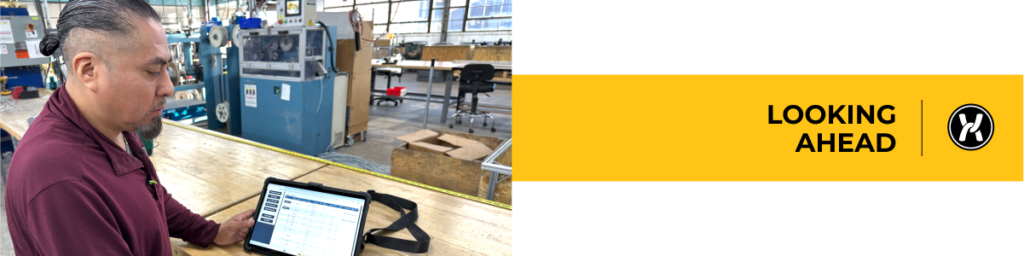
Looking Ahead
The journey to implement the ERP was not without hurdles. Many feature requests were implemented and improvements are ongoing. The team faced an initial adjustment period as employees adapted to the new system. However, the company’s planned approach, including a phased rollout and comprehensive employee training, ensured the system’s long-term success. Looking ahead, Lexco’s ERP system will be a cornerstone of its operations, enabling the company to provide exceptional service while remaining agile and forward-thinking.