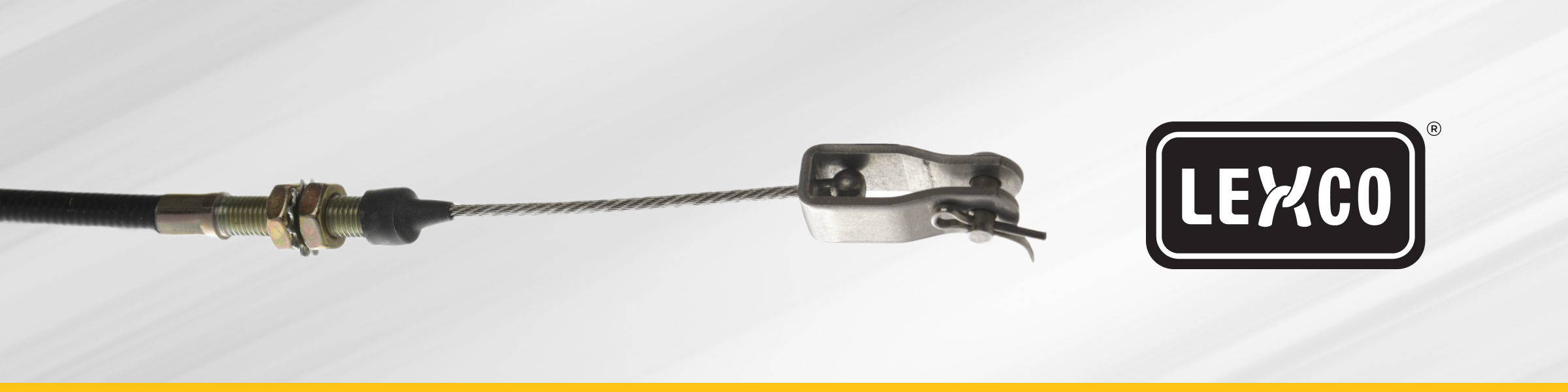
Understanding Push-Pull Controls
Push-pull controls are a wide class of mechanical controls that utilize cables that can be pulled or pushed for precise control. There are a wide variety of push-pull cables for many different applications, including the automotive, aerospace, and heavy machinery industries. These cables are used for adjusting and maneuvering control systems and play a critical role despite their relatively simple function. They are reliable and precise analog controls that are preferred for those applications where fast, intuitive, exact controls are required.
The design of push-pull control assemblies is complex, including the design of the cable subassembly itself. The engineering of a push-pull cable requires optimizing its lifespan, strength, functionality, and special requirements based upon the application. For example, control cables used for a plane’s rudder system will have different requirements than those used for bicycle brakes. This article will discuss the basics of push-pull controls, applications, and how to choose the correct cable for your specific needs.
How Push-Pull Controls Work
To understand how a push-pull cable system works, an overview of the basic structure of a push-pull cable assembly is required.
- Inner member: The core cable, which ensures the working load of the cable assembly.
- Conduit: The conduit or casing surrounding the core cable protects and guides the cable. A smooth, inner liner allows the cable to slide back and forth repeatedly without wear; conduit strands and a binding wire stop the whole assembly from snagging on other moving parts; and an outer sheath holds the whole thing together and provides additional wear protection.
- Conduit Cap: At each end of the cable assembly is an end cap that can be mounted to a control console surface and allows the transition of the cable conduit to the end rod.
- Seals: A swivel seal and wiper seal protect the inner cable assembly from the invasion of moisture or dust that could compromise its smooth operation. Seals also keep any inner lubricants from escaping.
- End Rod: The cable assembly terminates in a rigid rod (typically threaded) that connects to the application at one end and allows the controller to actuate the cable assembly at the other end.
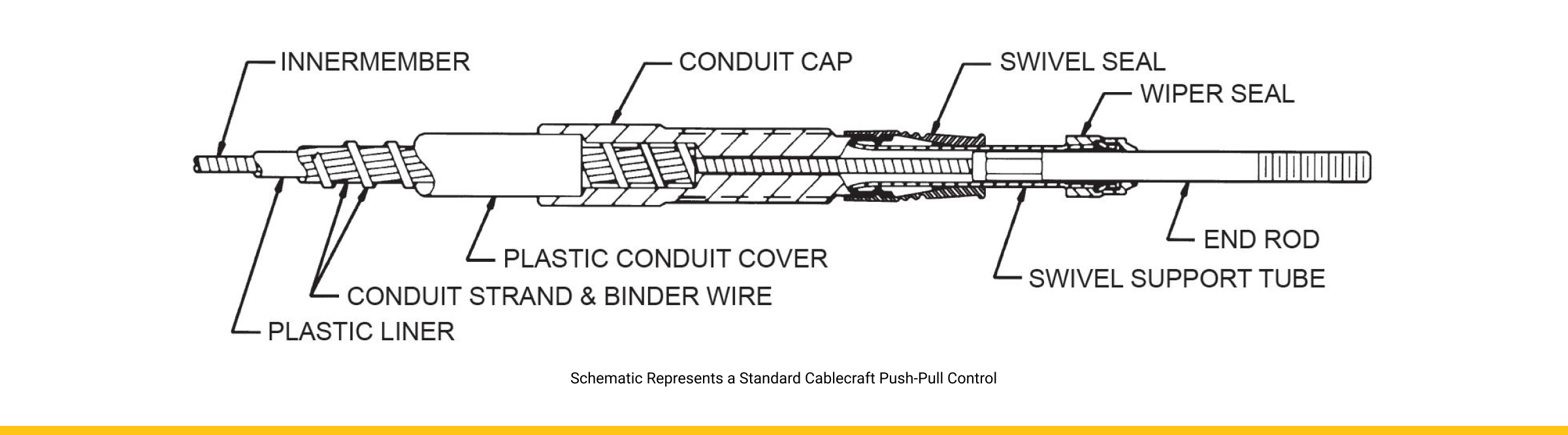
Options Available at Lexco®: Core Components and Materials
Lexco® Cable manufactures a wide variety of generic push-pull control cables and a high-quality line of Cablecraft® assemblies, with custom and non-standard options to support replacements or the design of OEM control schemes.
The basic design of push-pull control assemblies is the same, but customizations can vary widely based upon the application and the way in which the cable should be mounted or controlled.
- Pull-Only Controls: Many control cables are designed only to be pulled (i.e., bicycle brakes). These cables are designed with a flexible inner conduit and sometimes a spring that forces the assembly back to its neutral position when not pulled.
- Inner member Materials: Like many types of steel cable, the type of material used for the inner member matters to the final function. Galvanized steel provides greater strength with a corrosion-resistant coating, while stainless steel provides perpetual corrosion resistance that is also capable of operating in marine environments.
- Conduit Designs: Conduit design affects the final performance. The difference in rigidity and strength between bicycle conduit, bowden conduit, and long-lay conduit are all important for the cable’s ultimate use.
- End Fittings: End rod fittings such as adjustment nuts, wire stops, cable boots, equalizer plates, and non-threaded end caps are all important for designing the right control scheme.
- Alternate Control Schemes: Special control schemes, such as cables that can be actuated at both ends, hand lever controls, and foot control assemblies, are all available for Lexco’s line of Cablecraft cables.
- Control Heads: Specialized knobs, micro-adjustment heads, and latching mechanisms can be fitted for Cablecraft cables.
- Accessories: Ball Joint, Rod End, Strap Clevis, Yoke, Bellow, Compression Spring, Threaded Pivot, Wire Stop, Lever.
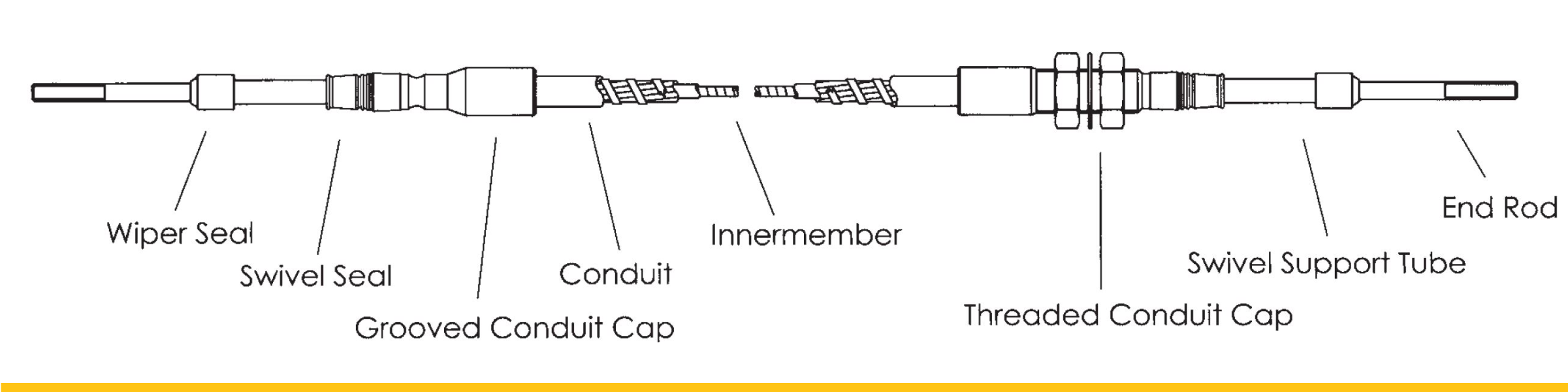
Generic Push-Pull Controls vs. Cablecraft® Push-Pull Controls
Generic push-pull controls are simpler, lighter-duty assemblies that are primarily used for pull applications. Generic push-pull controls often lack support tubes. In contrast, Cablecraft® push-pull controls are built for both push and pull functions, thanks to their support tubes.
Cablecraft® assemblies also feature armored inner cables, long lay conduit with binder wire wrap, and more frequent use of wiper seals. Additionally, Cablecraft® controls are typically pre-lubricated, while generic versions may not be lubricated.
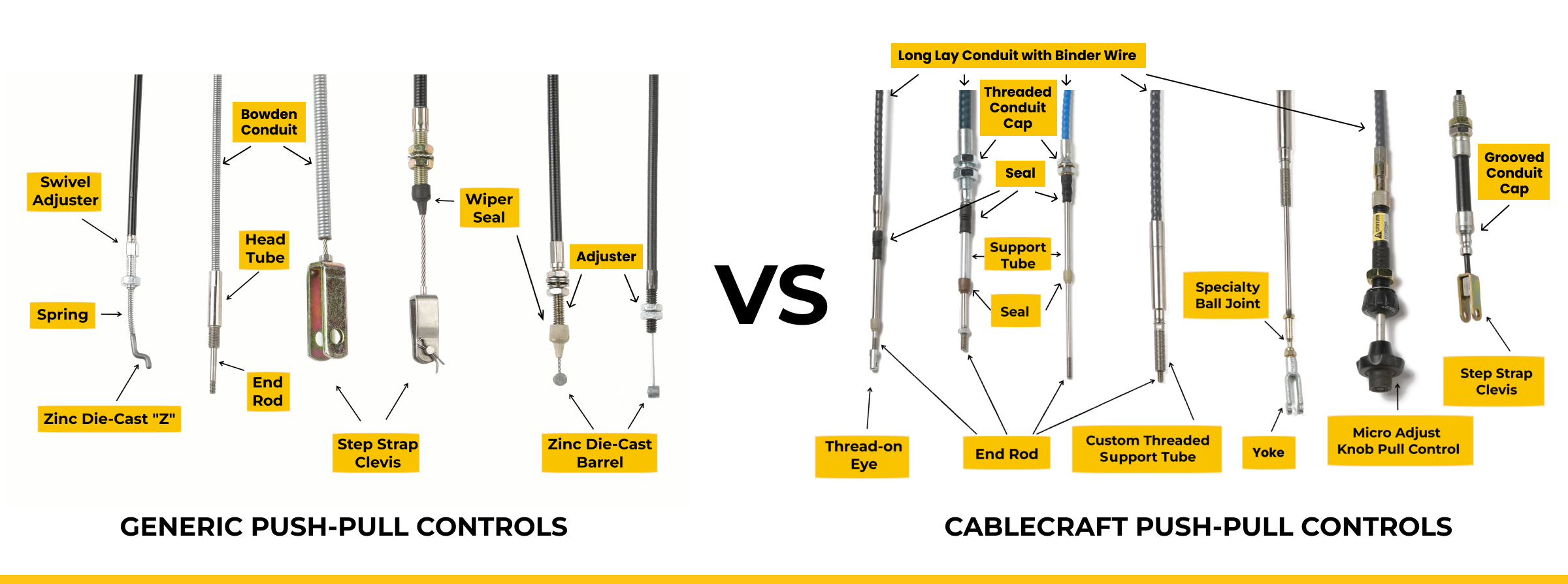
Applications Across Industries
The following are some of the most common and most important applications for push-pull cable controls:
- Aerospace: Push-pull control cables can be found in systems like landing gear mechanisms, throttle controls, rudder controls, aileron controls, and more.
- Military: Push-pull controls are utilized in ground vehicles such as tanks.
- Automotive: Automatic control systems like transmissions, brakes, shifting mechanisms, and air intake systems commonly utilize control cables.
- Heavy Industry: A wide variety of control levers, valves, maneuvering systems, adjustment mechanisms, and lifting systems utilize control cables for the actuation of mechanical and hydraulic systems.
- OEM: Latch controls, adjustment controls, emergency release controls, throttle controls, actuation controls, and many more.
- Marine: Core systems such as steering, water pumps, pressure control systems, and pull-start motors all use push-pull control cables.
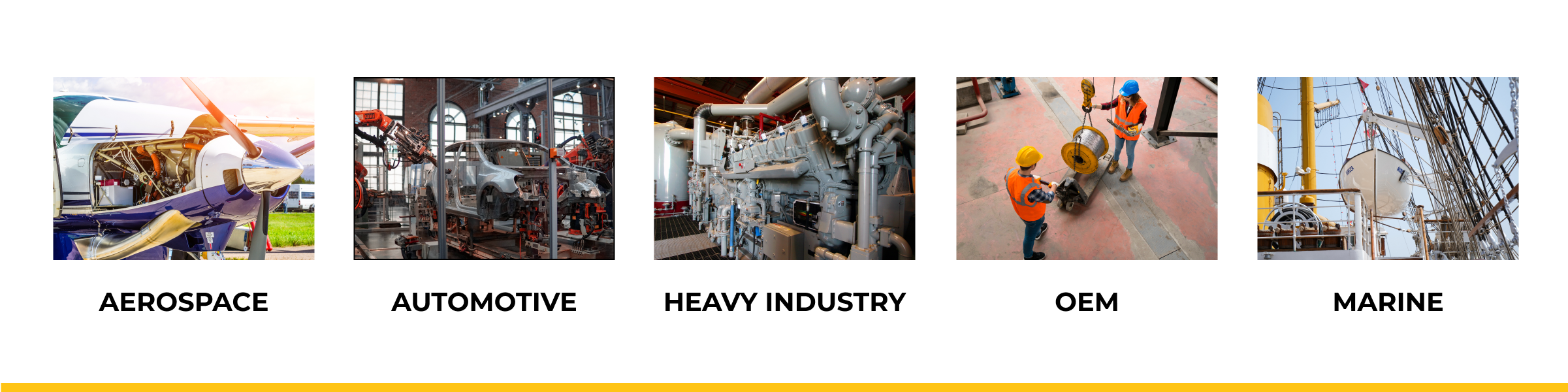
Choosing the Right Push-Pull Controls
When designing a push-pull cable control system, choosing the right cable assembly design is vital to ensure the optimal performance of the final system. There are several factors to consider when choosing the right cable design for your specific needs:
- Environment: Where will the cable be operating? Are there special requirements to resist corrosion or damage? Understanding where the cable will be installed ensures that it doesn’t prematurely fail.
- Loads: How strong must the cable be? Will the cable undergo significant forces in the pull and push directions or only one? A cable that is put under stress it cannot handle will fail quickly.
- Flexibility: What path will the cable take? Does its path require many bends? What is the min bend radius?
- Usability: Proper end fittings, control heads, and mounting assemblies allow an operator to more easily and more precisely use a control cable. Knowing how the cable will be used will help determine what the operator needs from the cable design.
Conclusion
Push-pull control cables are a key part of many control mechanisms across multiple industries. Designing and choosing the proper control cable assembly design takes into account many factors, from corrosion resistance to working load limit. Lexco Cable offers an extensive line of push-pull cables, design options, and high-quality cable customizations for most industries. Get a quote for your control cable designs from Lexco today.
PRODUCTS MENTIONED IN THIS BLOG