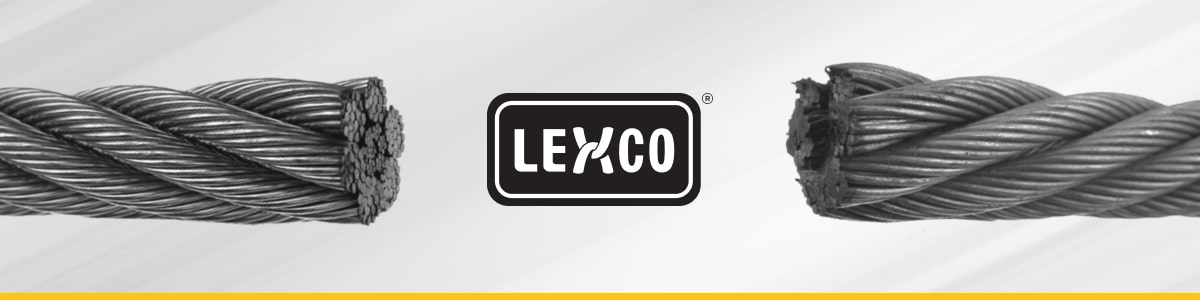
Why Choosing the Right Wire Rope Types Matter
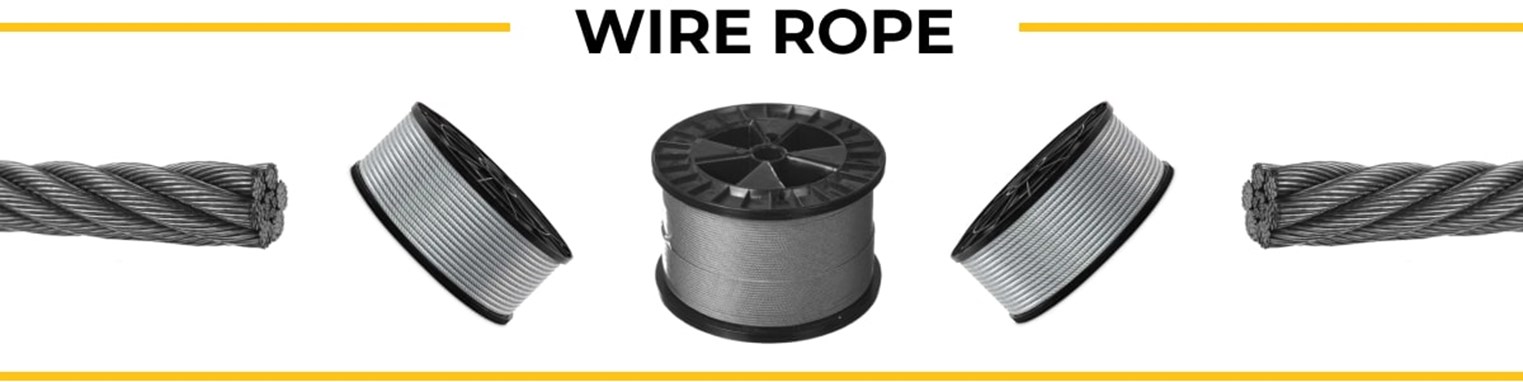
Have you ever witnessed your wire rope kinking, rusting, or fraying? Or perhaps found your wire rope twisting beyond what’s expected and wondered if it’s sufficiently rotation-resistant? Maybe you’ve been perplexed about why an assembly broke. Selecting the right wire rope types is not just about appearance or price—it’s about fit, form, and function.
The Clearance Conundrum
Ensuring you have the proper clearance can mean the difference between a smooth operation and unwanted friction or obstructions. For instance, if you’re setting up a pulley or sheave system, a rope that’s too thick might not fit the groove, compromising the entire operation. Similarly, if the wire rope is not centered in the groove of the sheave, it may wear prematurely. Always measure the required diameter against the space in which the rope will be used.
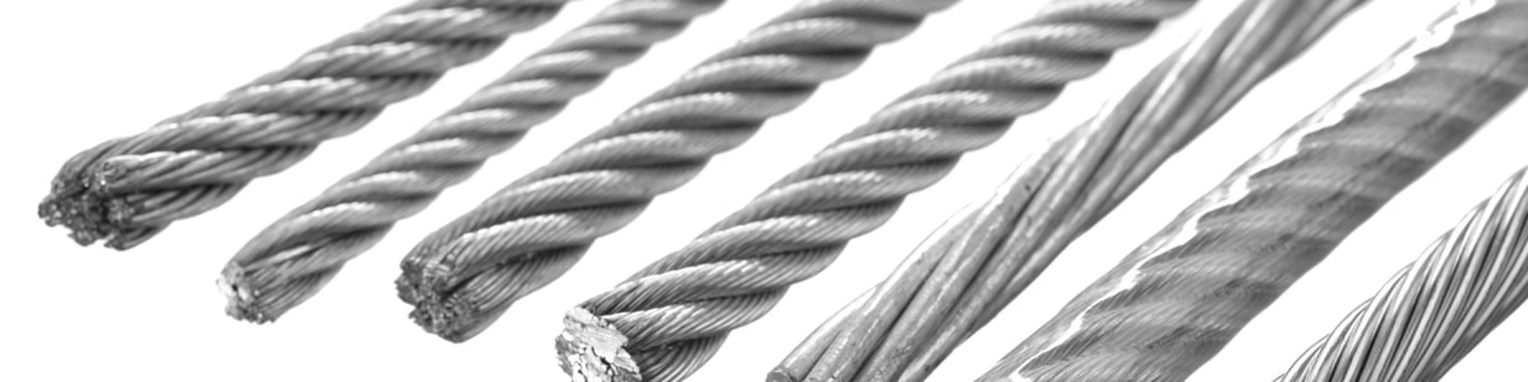
Strength – Deciphering MBS and WLL
Minimum Breaking Strength (MBS) refers to the nominal force at which a wire rope fails during a gradual pull, within a controlled environment pull-test. MBS is specified by a wire rope standard such as RR-W-410 and ASTM A1023. In case of an MBS inquiry, consult the material certificate and perform a pull test.
Warning: Never use a wire rope at MBS (or near MBS)
The Working Load Limit (WLL) represents the maximum load a wire rope can handle during regular use. While they might sound similar, they serve distinct purposes:
- 5:1 Safety Factor: Used primarily for general-purpose rigging, it means the MBS is five times the WLL. This is the norm for general lifting and hoisting tasks.
- 10:1 Safety Factor: Reserved for overhead loads, critical loads, and shock loads, the MBS is ten times the WLL, ensuring a higher margin of safety for more critical operations.
Note: If the wire rope termination pulls off before MBS, then WLL should be calculated based on terminal pull off strength. For example, consider 3/8″ 7×19 GAC with 14,400 lbs MBS. With full-strength efficiency terminations, 5:1 yields 2,880 lbs WLL. However, if the same wire rope assembly has end fittings that pull off at 10,000 lbs, then 5:1 becomes 2,000 lbs WLL.
Constructions to Know
Wire rope construction refers to the wire stranding pattern. How it’s constructed determines its characteristics and applications.
- 6×19 class meets RR-W-410 Type I, Class 2. Common 6×19 class constructions include:
- 6x19S (Seale): 6 strands with 19 wires per strand meets RR-W-410 Type I, Class 2, Construction 3.
- 6x25FW (Filler Wire): 6 strands with 25 wires per strand meets RR-W-410 Type I, Class 2, Construction 4.
- 6x26WS (Warrington Seale): 6 strands with 26 wires per strand meets RR-W-410 Type I, Class 2, Construction 5.
- 6×19 Class Recap: 6x19S, 6x25FW, 6x26WS are all 6×19 classification general purpose wire ropes.
- 6×37 class meets RR-W-410 Type I, Class 3. The most common 6×37 class is Construction 6 – 6x36WS (Warrington Seale).
- IPS is Improved Plow Steel.
- EIPS is Extra Improved Plow Steel and is synonymous with XIP or XIPS.
- IWRC is Independent Wire Rope Core.
- FC is Fiber Core.
* This list refers to specification standard RR-W-410
Flexibility and Bend Radius: Flexibility is an essential trait, especially if the rope undergoes frequent bending. Consider the bend radius to influence its longevity. The more wires which comprise the nominal diameter the more flexible the wire rope is. For example, 1/2″ 6×37 class is twice as flexible as 1/2″ 6×19 class. Fiber Core is more flexible than IWRC.
Torque and Rotation Resistance: Its construction impacts a wire rope’s resistance to torque and rotation. Make sure your choice complements its intended use. Rotation resistant wire ropes include 19×7, 8×19 class and 35×7 class.
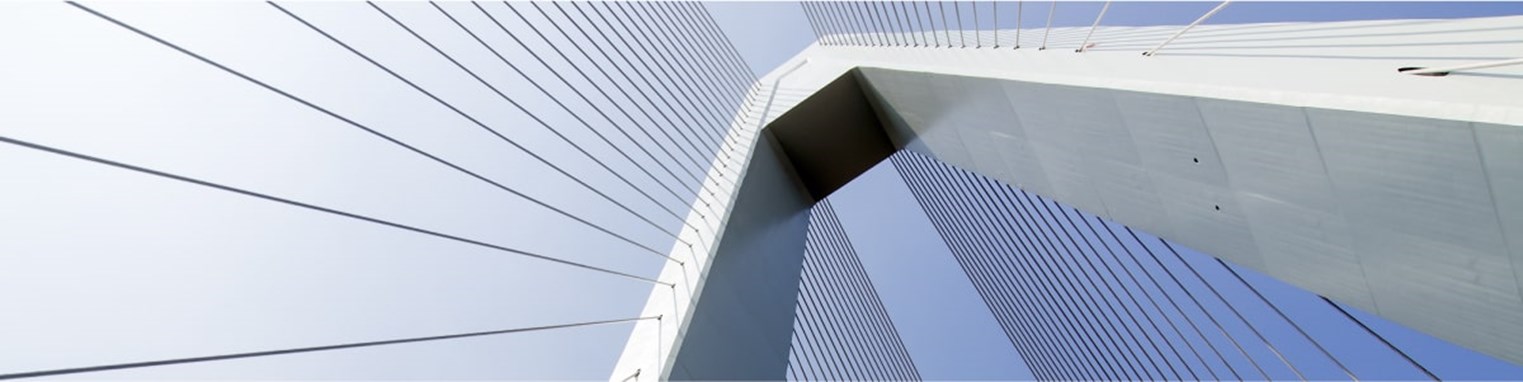
Wire Rope Material and Finish
Choosing between the available material and finish options isn’t just about appearance or cost. Each material and finish brings a unique set of benefits:
- Bright: The wire material is self-colored carbon steel finished with lube.
- Galv (Galvanized): Provides additional protection against corrosion, extending the life of your rope in challenging environments. Some galvanized wire ropes are dry and others are lubricated.
- Stainless: Resists rust and tarnish. Perfect for situations involving water or chemicals. Stainless Steel Type 304 and Stainless Steel Type 316 are typical.
- Coated: Jacketing offers protection and reduces wear, providing a smooth surface that might be easier on equipment and hands. Nylon coating is more abrasion resistant than PVC coating.
- Impregnated: Polypropylene infills between strands.
- Lubed: Reduces friction between wires, potentially prolonging the rope’s lifespan and reducing maintenance.
Value Added Assembly Fabrication
Terminations or end fittings play a pivotal role in a wire rope’s overall performance. It’s vital to ensure they’re adequately swaged. The quality and appropriateness of the fitting can determine the effectiveness and safety of the entire setup. But how can you ascertain that they’ll hold up to the nominal minimum break strength?
Beyond just choosing the proper fitting, there’s a need to understand its compatibility with the chosen rope. There’s also a need to consider whether they should be proof-loaded or even pull-tested
Safety – Above All
Wire ropes are often the lifeline in many operations. It’s essential to note that commercial-grade wire rope types 7×7 and 7×19, often referred to as aircraft cable, aren’t intended for aerospace applications. Using the wrong rope in aviation can lead to catastrophic results. But it’s not just aerospace—every application has its specific requirements.
For critical aerospace and defense applications, specifications like MIL-DTL-83420 are typically utilized to ensure that the wire rope (aircraft cable) will endure the rigors during intended use. MIL-DTL-83420 covers diameters 1/32″ through 3/8″.
Lay
Understanding the “lay” of a wire rope is crucial for ensuring its safe and effective use in various applications, from lifting and hoisting to towing and anchoring. The lay of a wire rope refers to the direction and manner in which both the individual wires and strands are twisted around the core. “Z” is a symbol representing right hand lay.
“S” represents left hand lay. 1×7 and 1×19 strands are typically left lay.
Right lay is most common for 7×7, 7×19, 6×19 class and 6×37 class strands. A mismatch between the lay of the rope and its intended use can result in uneven stress distribution, accelerated wear, and, ultimately, premature failure.
Experience – Wisdom from Failures
When a wire rope shows signs of wear, deformation, or outright fails, it’s a safety issue and a learning opportunity:
- What was the working load limit? This might indicate that the rope was overloaded.
- Was there a dynamic load? Dynamic loads can cause more stress than static ones.
- Was there an angular load or linear force? Angular loading significantly reduces strength.
- Was there a shock load? Sudden forces can strain even the toughest ropes.
- Did friction play a role? Over time, even minor friction can wear a wire rope down.
- Was the bend too tight? A tight bend can exert extra stress on particular rope sections.
- Was there corrosion? Even small amounts of corrosion can significantly weaken a rope.
- Were the end fittings swaged as required? Improper fittings can be a weak link in an otherwise strong chain.
Taking a step back to ask these questions and analyze failures can provide invaluable insights, ensuring better choices in the future.
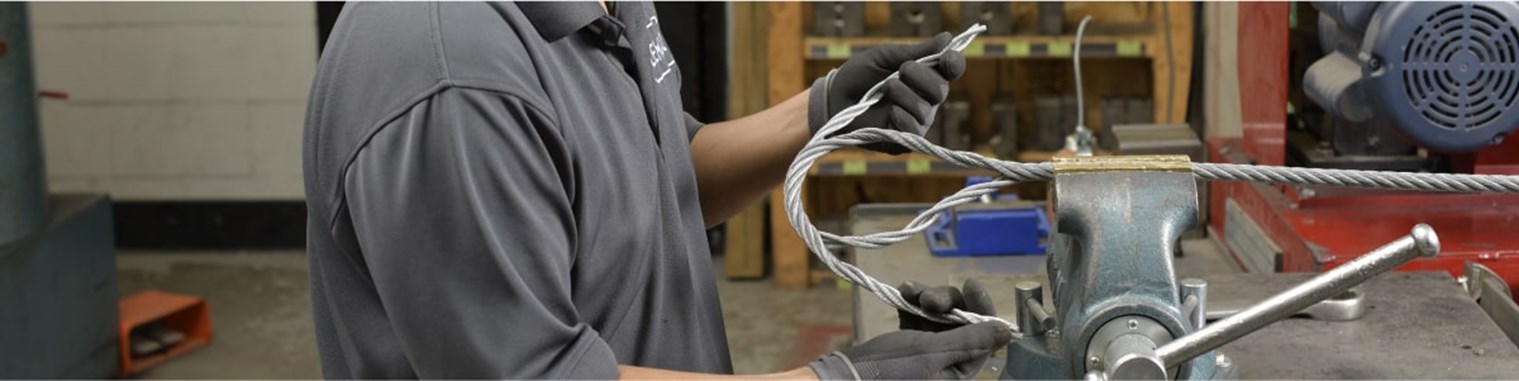
The Rope That Binds Success
All wire rope types have the potential for success or failure. The optimal selection for any application is about understanding a project’s nuances, applications, and demands. With the proper knowledge and a partner like Lexco® Cable by your side with engineer support, you’re not just choosing a wire rope—you’re setting the stage for success.
We look forward to working with you.